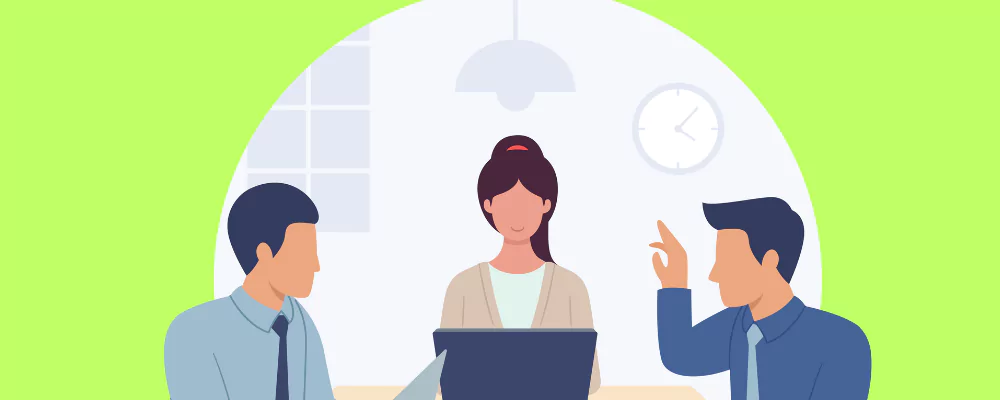
Waste oil treatment technology
Waste mineral oil refers to various types of waste oil, waste diesel, waste oil, waste oil, etc. generated in the maintenance of motor vehicles, tools, mechanical equipment, and the production and operation of industrial and mining enterprises. Waste
mineral oil has been listed in the National Hazardous Waste List (HW08). Waste mineral oil
mainly comes from the replacement of machinery, power, transportation and other equipment, oil residue and filter media.
Through the recycling and utilization of renewable energy, lubricating oil and other renewable resources, the recycling method can reduce environmental pollution, save energy and renewable resources, and achieve the purpose of sustainable development.
Common regeneration methods are as follows:
1.
Sulfuric acid-white clay method
According to the principle of oil-water refractory materials and water with a boiling point lower than that of oil, water is removed by heating and electrostatic separation, concentrated sulfuric acid is oxidized and dissolved, and the intermediate and colloid are oxidized to remove waste mineral oil, and activated white clay and activated carbon are used to adsorb pigments and insoluble sulfate macromolecular organic impurities, and mechanical impurities are removed by filtration to achieve the purpose of waste oil regeneration.
There is a lot of pollution from oil, low-yield oil and waste residue in this process.
In addition, there are many factors, such as the use of sulfuric acid, the lack of purity in the sulfuric acid market, and the difficulty of sulfuric acid transportation.
Now, this refining process has been replaced by other refining processes.
2.
Molecular distillation-clay refining method
This process uses the difference in the average free range of molecules of different substances to achieve the separation of substances.
The first heating, the energy is enough for the molecules to escape the liquid level, and the average free path of the molecules smaller than the light is greater than the average free path of the weight molecules to set the condensation surface, so that the light molecules are continuously condensed, and in this way the components we need are extracted from the waste oil, and finally the white clay is used for refining and decolorization.
The process can be operated at a temperature far below the boiling point, the distillation pressure is low, and the material is not easy to oxidize.
The light molecules released from the liquid surface reach the condensation surface almost without collision, so the heating time is very short, and the retention rate of volatile and heat-sensitive substances is high.
The operation is simple, the equipment is small, and the investment is less than the distillation process.
3.
Distillation-hydrogenation method
By adding hydrogen, some aromatic rings in the waste oil become cycloalkanes or open rings, and unsaturated compounds become saturated compounds, making the petroleum products lighter and more stable.
At the same time, the reaction of oil and hydrogen with non-hydrocarbons such as sulfur, nitrogen and oxygen will be controlled, and gases such as hydrogen sulfide, amines and water can be separated from oil, thereby improving the quality of the product.
It is a better method, with a higher hydrogenation yield instead of refined clay, and the output is higher than that of clay.
But the cost of investment, especially, is very high.
Generally speaking, small and medium-sized refineries do not have such conditions in terms of financial resources, and there are few domestic refineries.
At present, the vast majority of domestic waste ore recycling plants use the white grinding process of sulfuric acid, which has low recovery rate, high production efficiency and serious environmental pollution.